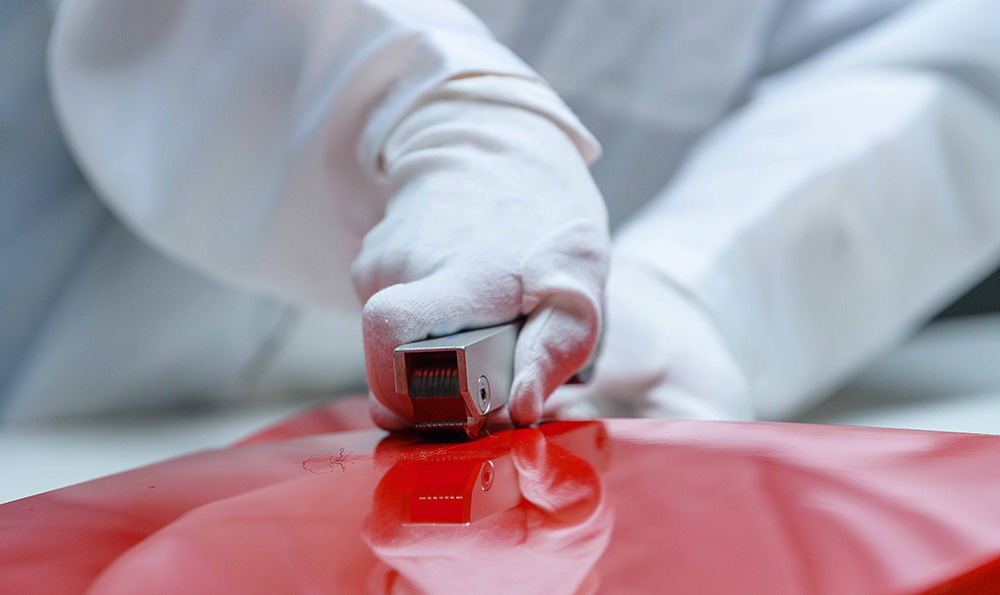
QUALITÄT
Die Alro Group bietet für Ihre Produkte stets die hochwertigste Qualität. Denn die Wertigkeit des Ergebnisses steht für uns an erster Stelle. Dafür sind wir auch im Markt bekannt.
Die Alro Group garantiert höchste Qualität dank eines internationalen Qualitätsmanagementsystems für die Automobilindustrie, das die Anforderungen von IATF16949 erfüllt. In diesem Zusammenhang werden jährlich unabhängige Audits durchgeführt, bei denen Bureau Veritas Certification die Zertifikate vergibt. Diese Zertifikate zeigen, dass die Alro Group ein zuverlässiger und professioneller Partner ist.
UNSERE VORGEHENSWEISE?
Zur Qualitätssicherung überprüft die Alro Group Ihre Spezifikationen in eigenen Labors. Hierbei kommen spezielle Geräte zum Einsatz, die reale Situationen simulieren. Neben dem Zentrallabor verfügt jeder Produktionsstandort über eines oder mehrere Prozess- und Qualitätslabors. Dort werden die Prozessparameter verifiziert und sämtliche grundlegenden Tests an den Lackschichten durchgeführt (Farbe, Glanz, Struktur, Haftung, Glätte, …). Zusätzlich können wir auch die technischen Eigenschaften der Beschichtung messen. So sind wir beispielsweise in der Lage, den Korrosionsschutz und die Beständigkeit gegen klimatische Einflüsse zu prüfen.
Darüber hinaus verfügen wir über das Know-how und die Ausrüstung für mikroskopische Analysen, um mögliche Defekte in der Beschichtung oder des beschichteten Produkts zu untersuchen. Weiterhin bestimmen wir auch die verschiedenen Schichtdicken in Mikron (1/1000 mm) mit höchster Präzision.
WELCHE TESTS WIR DURCHFÜHREN?
Visuelle Eigenschaften
Wavescan
Dieses Gerät misst die Struktur einer lackierten Oberfläche.
Glanzmesser
Dieses Gerät misst den Glanzgrad einer lackierten Oberfläche. Bei diesem Test messen wir die Reflexion von Licht.
Farbmessgerät
Mit diesem Gerät messen wir die Farbe und vergleichen sie mit der Masterplatte.
Dicke der Beschichtung
Magnetisch induktiv
Dieses Gerät misst die Gesamtschichtdicke einer lackierten Metalloberfläche.
Mikroskopie von Kunststoff und Metall
Durch die Anfertigung eines Querschnitts können wir die Schichtdicke aller einzelnen Farbschichten messen.
Kurztests
Erste Haftungstests: Gitterschnitttest
Bei diesem Verfahren wird die Lackschicht mit einem aus mehreren Schneiden bestehenden Gitterschnittmesser rasterförmig eingeschnitten. Danach wird mit Klebeband getestet, ob die Haftung bei den entstandenen Teilstücken erhalten geblieben ist. Für diesen Test existieren Parameter, die je nach Lacksystem und Kunde variieren können: der Abstand der Schneiden und der Klebebandtyp. Sie sind jeweils maßgeblich für den Rasterabstand bzw. die Klebkraft.
Erste Haftungstests: Ritzhärtetest
Bei diesem Test wird die Farbe mit der Klinge eines Taschenmessers abgeschabt. Danach wird die Glattheit der Ränder begutachtet.
Dampfstrahltest
Wir spritzen Wasser mit hohem Druck auf eine lackierte Oberfläche, die durch einen Kratzer beschädigt wurde. Die sich lösende Lackmenge und welche Schichten sich lösen ergeben ein Maß für die Haftung. Die Parameter können je nach Kunde variieren: Druck, Temperatur, Abstand der Düse zur Oberfläche, Größe der Düse, Dauer der Prüfung, bewegter oder stationärer Wasserstrahl, Art der Klinge, die den Kratzer erzeugt, Art des Kratzers (Kreuz, Streifen, kein Kratzer), …
Steinschlagtests
Bei diesem Test werden Steine mit Druckluft gegen ein Testobjekt geblasen. Die Anzahl der Einschläge in Kombination mit ihrer jeweiligen Größe und Tiefe sind ein Maß für die Haftung. Die Parameter können je nach Kunde variieren: Druck, Temperatur, Abstand zur Oberfläche, Menge der Steine, Art der Steine, Dauer des Tests, Aufprallwinkel (schräg oder gerade).
Langzeittests
Klimatests
Bei solchen Tests geht es um den Einfluss von Feuchtigkeit, Hitze und Kälte.
Kondenswassertest
Die Testobjekte verbleiben für eine bestimmte Zeit in einem Prüfschrank mit einer konstanten Temperatur von 40°C und einer Luftfeuchtigkeit von +/-100%, wobei sich auf den Flächen Kondenswasser bildet. Die je nach Kunde unterschiedlichen Parameter beziehen sich auf die Dauer des Tests (4 Tage bis 2 Wochen) und die Tests, die nach dieser Testdauer durchgeführt werden.
Wasserimmersionstest
Bei dieser Prüfung verbleiben die Testobjekte für eine bestimmte Zeit in einem Wasserbad mit einer bestimmten konstanten Temperatur. Die je nach Kunde jeweils unterschiedlichen Parameter beziehen sich auf die Dauer des Tests (2 Stunden bis 3 Wochen) und die Tests, die nach dieser Testdauer durchgeführt werden.
Konstante Wärme oder konstante Kälte
Hierbei verbleiben die Testobjekte für eine bestimmte Zeit in einem Ofen bei einer bestimmten konstanten Temperatur. Die je nach Kunde unterschiedlichen Parameter beziehen sich auf die Dauer des Tests (10 Tage bis 3 Monate) und die Tests, die nach dieser Testdauer durchgeführt werden.
Klimatests: Bewertungen
Die folgenden Parameter werden in der Regel nach einem der oben genannten Klimatests bewertet: Blasenbildung, Verfärbung, Veränderung des Glanzgrades und Verlust der Haftfestigkeit. Für einige Kunden ermitteln wir nach dem Test auch die Werte in Bezug auf Steinschlag und/oder Dampfstrahler. Bei Metall ermitteln wir u. a. die Rostbildung.
Korrosionstests
Neutraler Salzsprühtest (NSS)
Wir setzen die Prüfteile einem Salzwassernebel von neutralem pH-Wert bei einer zuvor erzeugten Beschädigung (Kratzer) aus.
Kupferbeschleunigtes Essigsäuresalzspray (CASS)
Wir setzen die Prüfteile einem Salzwassernebel und CuCI2 ⋅ 2H2O mit saurem pH-Wert bei einer zuvor erzeugten Beschädigung (Kratzer) aus. Dieser Test wird bei Aluminium angewendet.
Zyklischer Korrosionstest
Wir unterziehen die Prüfteile einem Programm, das aus einer Kombination von Salzsprühnebel oder einer Salzdusche (mit hohem Durchfluss), Feuchtigkeit, Temperaturschwankungen und Ruhephasen besteht. Auch hier erzeugen wir zuvor einen Schaden.
Zu den Parametern, die bei Korrosionstests je nach Kunde verschieden sind, zählen die Testdauer (3 Wochen bis 3 Monate), die Art der Prüfung (NSS, CASS, zyklischer Test), die Art des Kratzers (Kreuz, Streifen), die Breite des Kratzers, die Fließgeschwindigkeit der Salzlösung sowie die Tests, die nach der Testdauer durchgeführt werden sollen.
Korrosionstests: Bewertungen
Die folgenden Parameter werden im Allgemeinen nach einem der oben genannten Korrosionstests bewertet: Blasenbildung, Rostgrad / Blasenbildung an den Rändern, Rostgrad in der Fläche, Rostgrad / Blasenbildung um die erzeugte Beschädigung herum, Art des Rosts (rot, weiß, …) sowie Haftungsverlust.
Mikroskopische Fehleranalyse
Dies ist ein mikroskopischer Test. Hier analysieren wir den Staub auf der Fläche: in welcher Schicht befindet sich der Staub? Woher kommt er und welche Farbe hat er? So können wir ganz gezielt die Qualität von Lackierprozessen optimieren.
Mikroskopische Fehleranalyse für Kunststoffe
Für einen Querschnitt werden mit einem Skalpell sehr dünne Schnitte gesetzt.
Mikroskopische Fehleranalyse für Metall
Für einen Querschnitt werden Metallstücke eingebettet und dann geschliffen, bis der Fehler erreicht wird.
Für jeden Test existieren bestimmte Standards, die der Kunde im Vorhinein festlegt. Die Anforderungen und Prüfnormen richten sich danach, ob die Teile für den Innen- oder den Außenbereich dienen bzw. auch nach dem Teiletyp (Sichtteil, Fahrgestellteil, …), der Art des Lacksystems (KTL, Pulverbeschichtung, Nasslackierung) und ob es sich um Kunststoff oder Metall handelt. Der Kunde bestimmt beispielsweise auch, wie lange der Test laufen soll und wie lange gewartet werden soll, bevor die weiteren Tests durchgeführt werden. Auf diese Weise erfolgt bei Alro Group die Qualitätssicherung, damit ausschließlich hochwertige Produkte geliefert werden.